Introduction
RB-Technologies has been building and providing gas analyzers for combustion process management for 20 years. The purpose of the project is to develop a new combustion flue gas analyzer.
The sensor technology coming from diesel engine probes, thus needs troubleshooting. This sensor gives a specific response to the gas that will be measured, but SO2 gas is interfering with the measurement and must be eliminated from the flue gases before the latter reach the sensor.
First some SO2-absorbing materials were identified. Then we demonstrated that the chosen powder trapped SO2 when it was included in a specifically designed filter. This filter will affect the response time, so we must measure this effect to validate the method. Therefore, the response time of O2-probes, with or without SO2-filter was compared.
Experimental conditions
The O2 sensor is based on zirconium oxide semi-conductor technology. It produces a redox potential influenced by O2 concentration in flue gases, allowing us to measure O2 level without having to wait for a sampling.
Previous works have established that the probe response time is caused by three variables: The response time due to the filter in front of the sensor, the response time due to the sensor itself (mostly the polarization of the zirconium oxide), and the response time of the potential measurement electronic system. In order to free ourselves from the response time from the sensor and the electronic system, two identical sensors were submitted to the same conditions simultaneously. This allowed us to directly measure a difference in response time due only to the filters in front of the sensors.
Due to the high temperature both of the flue gas and the operating sensor, the probe must be built in temperature resisting materials such as inox316L and inconel600.
The SO2-filter was created by trapping some Mg(OH)2 (Sigma-Aldrich BioUltra 63081-250G-F, lot n°BCBR5830V) between two inconel-fiber filters in a threaded cylinder which can be adapted in front of the sensor (see Fig.1). The Mg(OH)2 powder obtained is 3.9 mm thick, with a minimum diameter of 28 mm.
As a comparison, two O2 probes were installed in the same chamber. One of the probes was protected by the SO2-filter, the other by an inconel-fiber filter device. The chamber was saturated with 1%O2 gas until the probes responses were stabilized. Then, the two probes were taken out in the open air (20.9%O2) together simultaneously.
The O2 responses (UO2) of the two probes were monitored with a recording voltmeter (Fuji Paperless Recorder ,type PHF51B11-E10EV-F SN°A7G7122T) and are given in Fig.2.
The experiment was repeated 3 times to obtain Δt60, the response time at 60% signal drop difference, with 95% confidence, by student law with two degrees of liberty, also given in Fig.2.
Results
As seen in Fig.2, the O2 response decreases exponentially in each case, which is a typical response for our sensors. The response time for a 60% signal drop difference was calculated. It is [4.6; 5.8] s, with 95% confidence. The response time is, as expected, significantly higher for the SO2-filter probe, but still in the same order of magnitude from the typical response time of our probes.
Conclusion
The response time difference with a SO2-filter is significant, as expected, but still in the same order of magnitude from a classical filter. This is therefore considered as reasonable for the needed applications, and is not considered as a failure factor for the project.
For future prospects, it must be specified that these results were obtained with a 4mm thick powder filter, which seems to be the order of magnitude not to exceed in order to keep a reasonable response time.
|
|
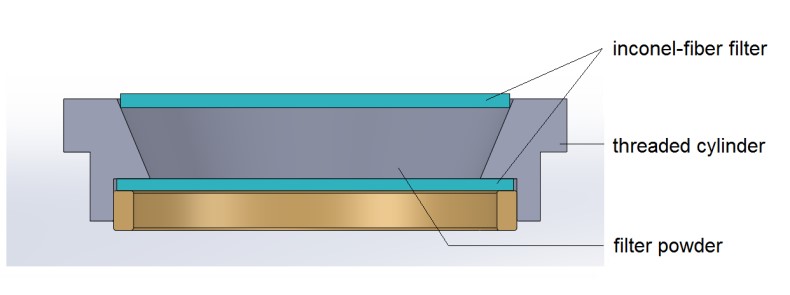
Figure 1: Drawing of the threaded cylinder (cross-section view) with anti-sulfur powder.
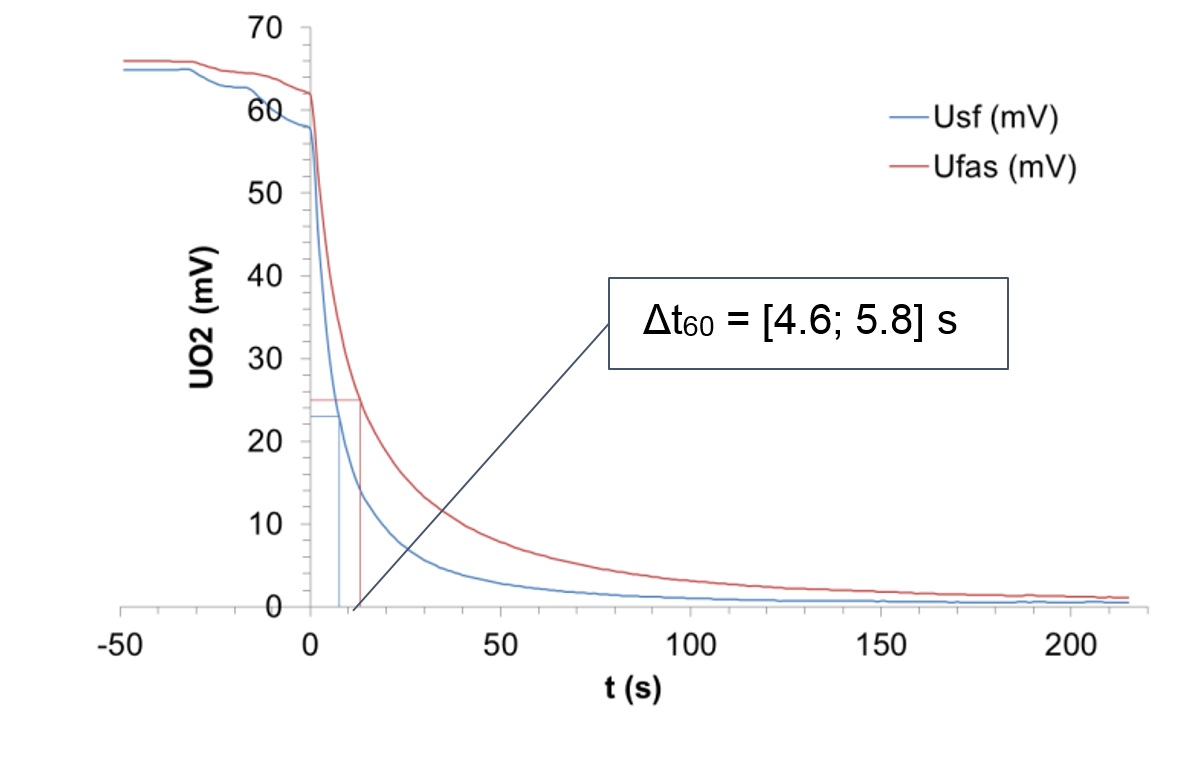
Figure 2: O2 responses of the probes with SO2-filter (Ufas) and without SO2-filter (Usf), and Δt60, response time for a 60% signal drop difference (with 95% confidence).
|